Understanding Chemical Vacuum Pump Operation
Ever wondered how certain processes achieve incredibly low pressures? The answer often lies in the ingenious workings of a chemical vacuum pump. These specialized pumps utilize chemical reactions to remove gas molecules from a sealed volume, achieving pressures far lower than mechanical pumps alone. This fascinating technology plays a crucial role in various fields, from scientific research to industrial manufacturing.
Unlike mechanical pumps that physically displace gas molecules, chemical vacuum pumps rely on chemical reactions to bind or trap these molecules. This allows for the creation of extremely high vacuums, essential for applications like materials science, analytical chemistry, and semiconductor fabrication. Understanding the fundamental principles behind chemical vacuum pumping is key to appreciating its significance in modern technology.
The core principle of a chemical vacuum pump revolves around the use of a getter material. This material, often a reactive metal, reacts with residual gases within the chamber, effectively removing them from the gaseous phase. This reaction converts the gas molecules into a solid or less volatile compound, thereby reducing the overall pressure within the system. Different getter materials are employed based on the specific gases targeted for removal.
The selection of the getter material is critical to the efficiency of the chemical vacuum pump. Factors such as the target pressure, the types of gases present, and the temperature of the system all influence this choice. Common getter materials include titanium, zirconium, and barium. These metals exhibit a high affinity for certain gases like oxygen, nitrogen, and hydrogen.
The history of chemical vacuum pumps is intertwined with the development of vacuum technology itself. Early experiments with gettering materials laid the foundation for the sophisticated chemical vacuum pumps we see today. As scientific and industrial demands for higher vacuums increased, so too did the development and refinement of these specialized pumps.
A simple example of a chemical vacuum pump's function can be seen in the production of incandescent light bulbs. After the air is evacuated, a getter material is often used to absorb any remaining gas molecules, preventing filament oxidation and prolonging the bulb's lifespan.
One key benefit of chemical vacuum pumps is their ability to achieve extremely low pressures, often exceeding the capabilities of mechanical pumps. Another advantage is their compact size, making them ideal for integration into smaller systems. Furthermore, they require less maintenance compared to mechanical pumps, contributing to lower operational costs.
To maximize the effectiveness of a chemical vacuum pump, it's crucial to ensure the proper selection of the getter material based on the specific application. Regular monitoring of the pump's performance is also essential for identifying any potential issues. Lastly, maintaining a clean and contamination-free vacuum system is vital for optimal performance.
Common challenges related to chemical vacuum pumps include the limited capacity of the getter material, which can become saturated over time. Solutions include regenerating the getter or replacing it with a fresh supply. Another issue can be the generation of heat during the chemical reaction. Implementing effective cooling mechanisms can address this.
Advantages and Disadvantages of Chemical Vacuum Pumps
Advantages | Disadvantages |
---|---|
Achieves ultra-high vacuum levels | Limited getter capacity |
Compact size | Potential for heat generation |
Lower maintenance requirements | Getter material specificity |
Frequently asked questions about chemical vacuum pumps include: How do they differ from mechanical pumps? What are the common applications? How do you choose the right getter material? What is the typical lifespan of a getter? How do you maintain a chemical vacuum pump? What are the safety considerations? What are the cost implications? How does temperature affect performance?
Tips and tricks for working with chemical vacuum pumps include ensuring proper system preparation before activation, carefully handling the getter material, and monitoring the vacuum level regularly.
In conclusion, the chemical vacuum pump working principle provides a unique and powerful method for achieving ultra-high vacuums. Its reliance on chemical reactions, rather than mechanical displacement, opens doors to a wide range of applications where precise control over pressure is essential. From scientific research to industrial manufacturing, the ability to create and maintain extremely low pressures has revolutionized countless processes. While challenges like limited getter capacity exist, ongoing advancements in getter materials and pump design continue to improve performance and broaden the applications of this fascinating technology. Understanding the working principles, benefits, and best practices associated with chemical vacuum pumps is crucial for leveraging their full potential and pushing the boundaries of vacuum technology. By continually refining our understanding and implementation of these principles, we can unlock new possibilities in diverse fields and further advance the frontiers of science and engineering.
The enduring appeal of urban bronze exterior paint
The allure of the anime bad boy image
Yamaha 99 outboard electric start the ultimate guide



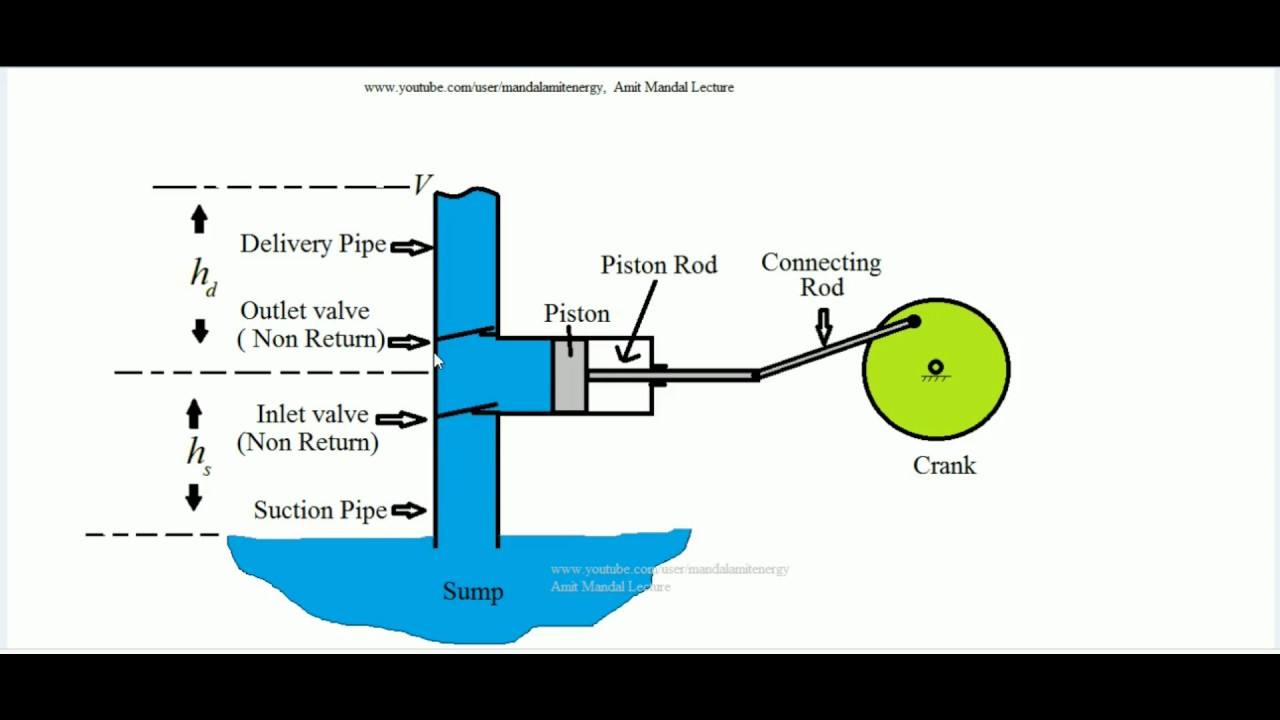

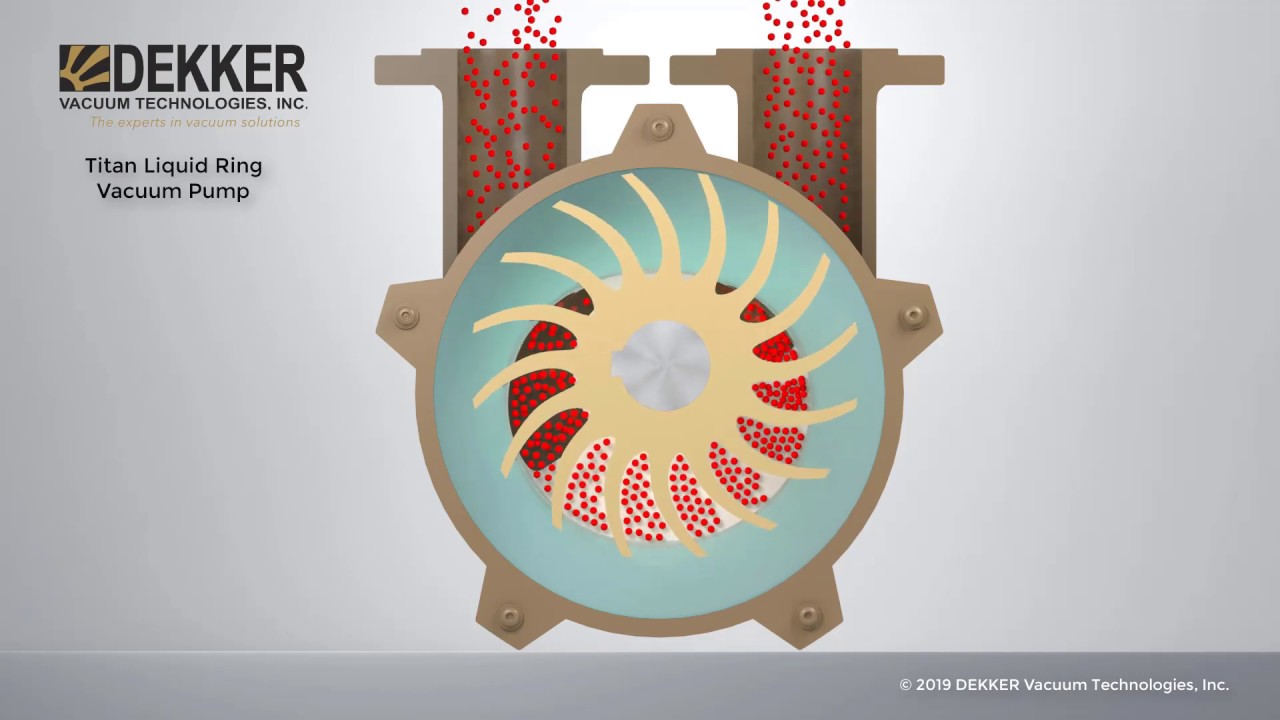





