Decoding the Secrets of Liquid Level Switch Symbols
Imagine a world without clear indicators telling you when your water tank is full or your fuel tank is nearing empty. Chaos, right? That's where the humble yet critical liquid level switch symbol comes into play. These small graphic representations communicate vital information about the amount of liquid in a tank or container, preventing overflows, dry runs, and potentially hazardous situations.
Liquid level switch symbols are the silent guardians of countless industrial processes, from the mundane to the mission-critical. They're the visual shorthand that keeps everything flowing smoothly, ensuring efficiency and safety in applications ranging from simple household appliances to complex chemical processing plants. But what do these symbols actually mean, and why are they so important?
Understanding liquid level switch symbols is akin to learning a new language. Each symbol represents a specific type of switch and its function, conveying information about the level at which the switch activates. This visual language allows operators and engineers to quickly assess the liquid level status and take appropriate action. Whether it's a simple float switch in a toilet tank or a complex capacitance probe in a chemical reactor, the underlying principle remains the same: to provide a clear, concise indication of the liquid level.
The history of liquid level indicators dates back centuries, evolving from simple visual inspections to sophisticated electronic sensors. Early methods involved dipsticks and sight glasses, providing direct but often inconvenient means of checking liquid levels. The advent of float-activated switches marked a significant advancement, enabling automatic control of liquid levels. Today, a wide variety of liquid level switch technologies exist, each with its own unique symbol representing its functionality and operating principle.
The core issue surrounding liquid level switch symbols is the need for standardization. While there are some commonly recognized symbols, variations and inconsistencies can lead to confusion and misinterpretation. This is particularly crucial in safety-critical applications where misreading a symbol could have serious consequences. Therefore, a clear understanding of the specific symbols used in a given system is essential for safe and efficient operation.
A simple example is the symbol for a normally open (NO) float switch. This typically depicts a switch contact that is open (disconnected) when the float is at its lowest position and closes (connects) when the liquid level rises, lifting the float. Conversely, a normally closed (NC) float switch symbol shows a closed contact at the low level and an open contact at the high level.
Benefits of standardized liquid level switch symbols include improved safety, reduced operator error, and enhanced system maintainability. Clear, unambiguous symbols minimize the risk of misinterpreting liquid level information, preventing accidents and ensuring efficient operation. Standardized symbols also facilitate troubleshooting and maintenance by allowing technicians to quickly identify the type and function of each switch.
A simple checklist for understanding liquid level switch symbols involves identifying the type of switch (e.g., float, pressure, capacitance), its normal state (NO or NC), and the activation point (high level, low level, or intermediate levels). This information, often embedded in the symbol itself, provides a quick overview of the switch's functionality.
Advantages and Disadvantages of Different Liquid Level Switch Technologies
While many types of switches exist, comparing float and capacitance provides a good overview of the symbol differences and implications.
Feature | Float Switch | Capacitance Switch |
---|---|---|
Symbol | Typically depicts a float and a switch contact. | Often uses a stylized capacitor symbol. |
Advantages | Simple, reliable, cost-effective. | Can detect a wide range of liquids, including non-conductive liquids. |
Disadvantages | Can be affected by turbulence and buildup. | Can be sensitive to changes in dielectric constant of the liquid. |
Best practices for implementing liquid level switches include proper selection based on the application, regular maintenance and calibration, clear labeling of symbols, and comprehensive operator training. Ensuring that operators are familiar with the symbols used in their specific system is crucial for preventing errors and maintaining safety.
Frequently asked questions about liquid level switch symbols often revolve around the meaning of different symbols, their application in specific industries, and troubleshooting common problems. Resources such as online forums, manufacturer websites, and industry-specific guides can provide valuable information.
In conclusion, liquid level switch symbols play a vital role in ensuring safe and efficient liquid management across a wide range of applications. From preventing overflows in simple household appliances to managing complex chemical processes in industrial plants, these seemingly small symbols have a significant impact. Understanding and properly implementing liquid level switch symbols is essential for maximizing system performance, minimizing risks, and ensuring smooth operation. By embracing standardized symbols, promoting clear communication, and emphasizing the importance of operator training, we can unlock the full potential of these crucial indicators and further enhance the safety and efficiency of our liquid handling systems. Remember, these small symbols are not just lines on a diagram – they represent a critical layer of safety and control in countless industrial processes, making them worthy of our attention and understanding.
Decoding software bugs a comprehensive guide
Navigating indiana roads the essential drivers handbook
Is the toyota rav4 really a mid size suv lets investigate

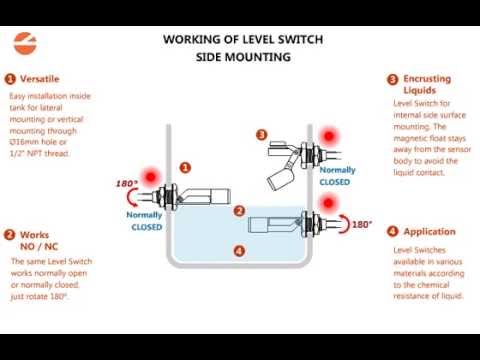












